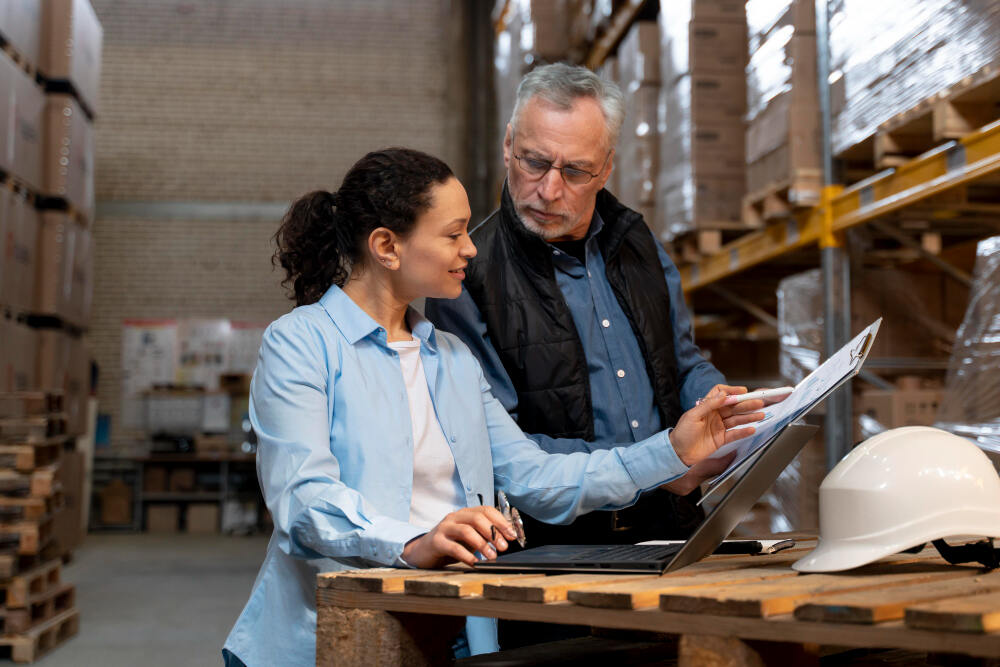
Raw Material Inventory Management: Manufacturer’s Guide
What is Raw Material Inventory Management?
Raw material inventory management is a process in which you can manage the material goods that are used to create different products. This ensures that you already have enough raw material to make up for the demands and to avoid operational lost time.
If you control the inventory levels of raw materials, you can achieve two goals:
You can save money
You can complete production jobs and complete orders faster
Raw material inventory management involves different processes such as tracking, consuming, purchasing, and relocating raw materials.
Examples of Raw Material Inventory
Raw material inventory includes the ingredients that the manufacturer uses to produce the products. There are two types of raw materials that are used to make products
1-Direct materials
It refers to the material that is directly used to make products. For example, if you want to make LED light the direct raw material would be LED boards, connection wires, soldering flux, LED chips, and rectifier circuits.
2- Indirect materials
These are the supplementary items that are used to produce that specific product. In the making of LED lights, the indirect material will be drill bits, disposable gloves, mops, and detergent.
Why is Raw Material Inventory Management Important?
It is important for the manufacturers because it directly impacts the productivity and efficiency of the workflow. You can make better decisions for your sales if you know the location, value, and quantity of your stocked raw material. It will overall enhance your productivity.
But in case you do not implement inventory management of raw materials, your manufacturing cost will increase and productivity will decrease. So implement this strategy to ensure production.
Raw Material Inventory Management Challenges
The focus biggest challenges are as follows
1- Inventory Planning
This challenge can be caused by many factors such as product lead time, demand variability, and supply chain disruption. Poor planning can also be risky as it results in overstocking of goods which is also a waste and overstocking means you are not able to fulfil the demands of your customer.
Inventory management should be effective it must contain demand forecasting tools, and an optimized warehouse, and it should be accurate. This all will improve inventory planning.
2- Financial Constraints
It is also a bigger challenge that you lose the opportunity to invest in bulk raw materials. It also affects your delivery time with suppliers. When the budget is short, your ability to get benefits in bulk is reduced. To overcome this, you need to minimize the capital tied up by accurate demand planning and well warehouse management.
3- Reliance on a Few Suppliers
If you have reliance on a few suppliers, you can face the issues. You must have backup suppliers to support your business. Suppliers increase the productivity of your goods so they must be active and in bulk.
4- Quality Control
The consistent quality of raw materials is a challenge to maintain. It is very important for the manufacturers to maintain quality like freshness and food safety. The quality determines the value of your product so it must be of high quality. Raw material inventory management ensures the quality of raw materials.
How to Manage Raw Material Inventory?
There are five techniques that are used to manage raw material inventory.
1- Just-in-time JIT
This technique helps in reducing the cost of manufacturing goods. It overall improves productivity and reduces wastage as it produces only when it’s needed.
2- Demand Forecasting
This technique determines your future needs for the stock that is based on the previous performance and factors. It ensures that you have the right amount of inventory to satisfy your customer demand.
3- Economic order quantity
It involves the ordering, holding, and storage costs of inventory. EOQ helps reduce the cost of inventory by establishing the ideal order quantity of raw materials. With this technique, you will have sufficient supply to meet the customer’s expectations.
4- Six Sigma
This technique reduces inventory defects and variations. It is basically a data-driven approach that uses statistical analysis to remove unnecessary steps and improve the efficiency of inventory management.
5- Materials Requirement Planning
It is a sales-forecast-dependent method that is used to estimate the quantities of raw material required to fulfill your customer’s demands.
Practices to Manage Raw Material Inventory
1- Develop a system of SKU
You can allocate a unique code to each inventory item. Stock keeping unit is considered the basis of inventory management as it helps you track the inventory movements and stock levels.
2- Inventory Control System
A good control system tracks and manages the inventory levels, raw materials reorder, and raw materials inventory lead items.
3- Data-driven approach
Data-driven approach improves inventory management as it provides an accurate picture of inventory status. It also helps you in making informed decisions for your inventory management.
4- Automating Operations
The automation process helps you reduce errors and provides you with accurate reports of inventory management operations. Overall it will increase your production process.
5- Focus on Raw Material
You can use KPIs and inventory ratios to check which item is necessary and will benefit your business. It helps you in finding the best raw material for your products.
Inventory Accounting for Raw Materials
Inventory accounting refers to the total expenses or the costs that have not been used in the production process and you have on your hand. It gives you an insight into your financial health and tracks your investment throughout the inventory process.
Metrics for Raw Material Accounting
1- Inventory turnover Ratio
This ratio helps you determine that you have more inventory than the amount you are selling. It also measures how many times you have sold or replaced your raw material stock.
2- Days on Hand
It measures the rate of your inventory on a daily basis. This metric also determines how effectively you are using your raw materials inventory
3- Weeks on Hand
This shows the inventory sales on a weekly basis. Fewer weeks on hand show the efficiency of inventory and more weeks on hand show the inefficiency of stock.
How to Calculate Raw Material Inventory Value?
You can add opening inventory to net purchase inventory and subtract the total cost of goods sold.
Opening inventory + Net purchase inventory – COGS=Ending
Raw Material Inventory Management Software
This software helps you to streamline all the inventory processes and optimize inventory management.
Key features of this software include
- User-friendly- accessible to anyone and easy to navigate.
- It is scalable as it grows with your business.
- It can be integrated with other business modules, software, and applications.
- Secured to protect your personal information.
Final Thoughts
Raw material inventory management is a process of handling, storing, and procuring raw materials. It maintains the optimal level of raw material inventory. It has a crucial role in managing the inventory and manufacturing processes. Hope this blog will guide you in all the concerned aspects of the inventory management system!